- Актуальные нормативные документы
- ГОСТ 285-69: ключевые требования к проволоке
- Международные аналоги (DIN, ASTM, ISO)
- Критерии проверки качества
- Контроль диаметра сердечника и шага шипов
- Тестирование защитного покрытия: оцинковка vs ПВХ
- Практические методы оценки
- Визуальный осмотр на дефекты плетения
- Измерение усилия на разрыв в полевых условиях
- Распространённые нарушения при производстве
- Несоответствие заявленной маркировке
- Снижение коррозионной стойкости
Актуальные нормативные документы
На территории Украины и стран СНГ производство колючей проволоки регламентируется четкими нормативами. Эти документы определяют ключевые параметры изделий и методы их испытаний. Большинство производителей ориентируются на советские ГОСТы, которые по-прежнему остаются эталоном качества.
Производственный контроль основывается на нескольких документах. Помимо основного ГОСТ 285-69, применяются ГОСТ 3282-74 для проволоки-основы и ГОСТ 9.315-91 для оценки защитных покрытий. Комплексное соответствие всем этим нормативам гарантирует долговечность и функциональность изделия.
ГОСТ 285-69: ключевые требования к проволоке
ГОСТ 285-69 — базовый документ, регламентирующий характеристики колючей проволоки. Действует с 1969 года с минимальными изменениями. Он устанавливает жесткие требования к геометрии и прочностным показателям.
По данному стандарту диаметр проволоки-основы должен находиться в диапазоне 1,6-2,5 мм. Колючки изготавливают из проволоки с сечением 1,6-2,0 мм. Расстояние между шипами регламентируется в пределах 75-100 мм. Отклонение не может превышать ±10 мм.
Прочностные характеристики тоже строго нормированы. Временное сопротивление разрыву должно составлять не менее 380-500 МПа в зависимости от типа проволоки. Изделие выдерживает нагрузку 900-1000 Н без разрушения.
ГОСТ предусматривает два основных типа защитных покрытий. Первый — цинковое покрытие с толщиной слоя не менее 20 мкм или массой 150-200 г/м². Второй — покрытие из ПВХ толщиной 0,4-0,5 мм. Дополнительно производится тест на адгезию и эластичность покрытия.
Проволока классифицируется на два типа: обычная двухосновная и режущая одноосновная. Последняя имеет шипы с усиленными режущими кромками и применяется в условиях повышенных требований к защите периметра.
Международные аналоги (DIN, ASTM, ISO)
В международной практике колючая проволока регламентируется несколькими стандартами. Они имеют свои особенности и акценты в методологии оценки качества.
DIN 1548 — немецкий стандарт, применяемый в ЕС. Он более либерален к форме шипов, но жестче к антикоррозионной защите. Требует оцинкование с покрытием 350-380 г/м², что в 1,5-2 раза выше украинских норм. Основной акцент сделан на экологичность и долговечность.
Американский стандарт ASTM A121 делит колючую проволоку на четыре класса прочности. Низший класс 1 соответствует обычной проволоке с прочностью 350-400 МПа. Высший класс 4 предназначен для военных объектов с прочностью до 1200 МПа. Особенность — допустимость большего разброса в размерах шипов (до ±15 мм).
ISO 22413 объединяет требования американских и европейских стандартов. Документ регламентирует не только физические свойства, но и методы испытаний. Для проверки коррозионной стойкости применяется жесткий тест в соляном тумане — 720 часов без признаков красной ржавчины.
В отличие от ГОСТ, международные стандарты допускают использование специализированных сплавов. Например, проволока из нержавеющей стали AISI 316 с высоким содержанием молибдена для применения в морском климате или сплавы на основе алюминия для специальных задач.
Критерии проверки качества
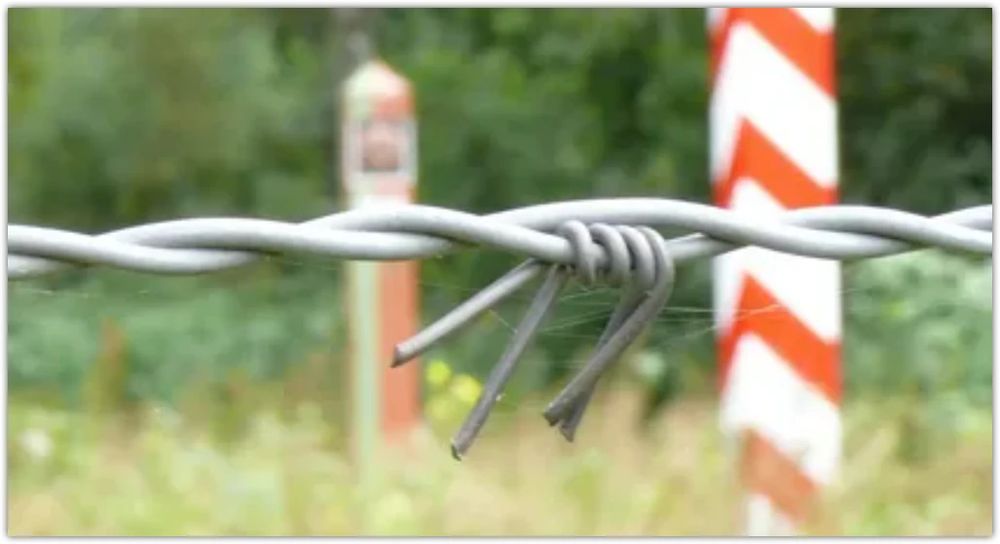
Оценка качества колючей проволоки проводится по строго определённым параметрам. Многоступенчатый контроль включает измерение геометрических показателей, физических свойств и защитного слоя. Каждый из этих показателей влияет на эксплуатационные характеристики.
Производственная лаборатория применяет целый арсенал измерительных инструментов. Микрометры, штангенциркули, разрывные машины — всё это составляет основу технического контроля. Комплексная проверка позволяет выявить отклонения от номинальных значений.
Контроль диаметра сердечника и шага шипов
Диаметр проволоки измеряют микрометром с ценой деления 0,01 мм. Замеры выполняют в нескольких точках. Допустимое отклонение составляет ±0,05 мм для основной проволоки и ±0,04 мм для шипов.
Выборочный контроль предусматривает не менее десяти измерений на каждые 500 кг продукции. При обнаружении даже одного несоответствия партию отправляют на сортировку. Этот параметр напрямую влияет на разрывную прочность изделия.
Шаг расположения шипов должен соответствовать заявленному типу. Колючка типа КЦ-1 имеет шаг 50-125 мм, КЦ-2 — 100-125 мм. Замеры проводят металлической линейкой или специальным шаблоном с эталонными расстояниями. Неравномерность расположения шипов снижает защитные свойства и создаёт “мёртвые зоны”.
Форма шипов проверяется визуально и тактильно. Острота заточки оценивается по углу схождения граней — не менее 35-40°. Длина шипа от основы до вершины составляет 10-22 мм в зависимости от типа проволоки. Затупленные или деформированные шипы существенно снижают эффективность заграждения.
Тестирование защитного покрытия: оцинковка vs ПВХ
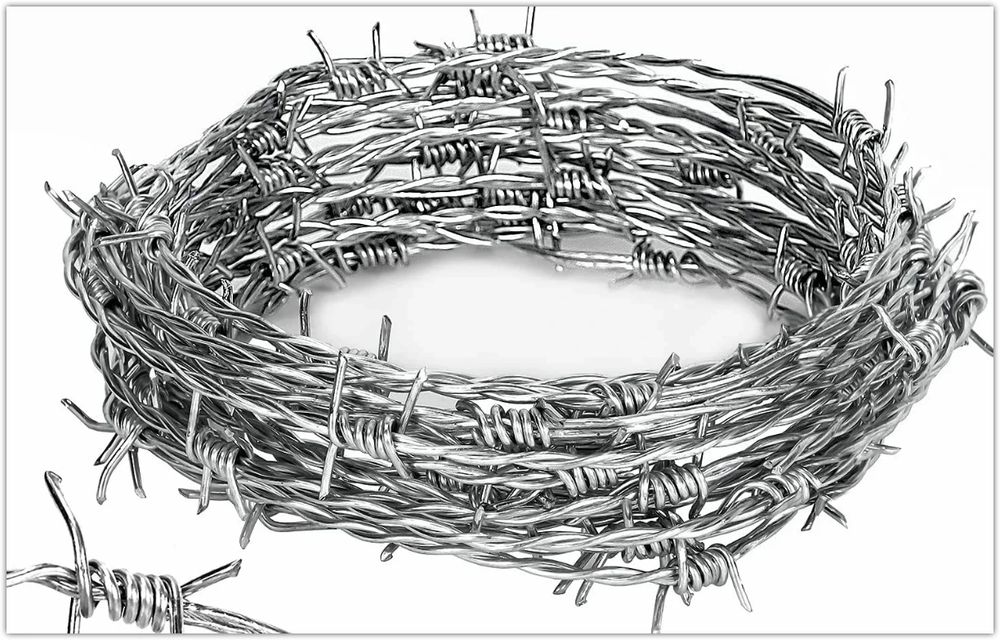
Оцинкованная проволока тестируется на толщину слоя и адгезию. Стандартный метод — взвешивание до и после удаления цинка химическим способом. Разница масс позволяет вычислить граммаж покрытия на квадратный метр.
Ускоренные коррозионные испытания проводят в камере соляного тумана. Образцы подвергают воздействию 5% раствора хлорида натрия при температуре 35°C. Для первого класса покрытия время до появления продуктов коррозии должно составлять не менее 96 часов.
ПВХ-покрытие проверяют на эластичность методом намотки. Образец наматывают на цилиндрический стержень диаметром, равным шестикратному диаметру проволоки. На поверхности не должно возникать трещин, отслоений или других дефектов.
Толщину полимерного слоя измеряют магнитно-индукционным или ультразвуковым толщиномером. Допуск составляет ±0,05 мм. Недостаточная или неравномерная толщина покрытия приводит к ускоренной коррозии металла основы.
Устойчивость к ультрафиолету — важный параметр для ПВХ-покрытия. Тест проводят в специальной ксеноновой камере, имитирующей солнечное излучение. После 1000 часов воздействия допускается незначительное изменение цвета, но не должно быть растрескивания или потери эластичности.
Адгезия покрытия оценивается методом решетчатых надрезов. На поверхности делают перпендикулярные надрезы с шагом 1 мм, затем наклеивают и отрывают липкую ленту. Допускается отслоение не более 5% площади ячеек.
Практические методы оценки
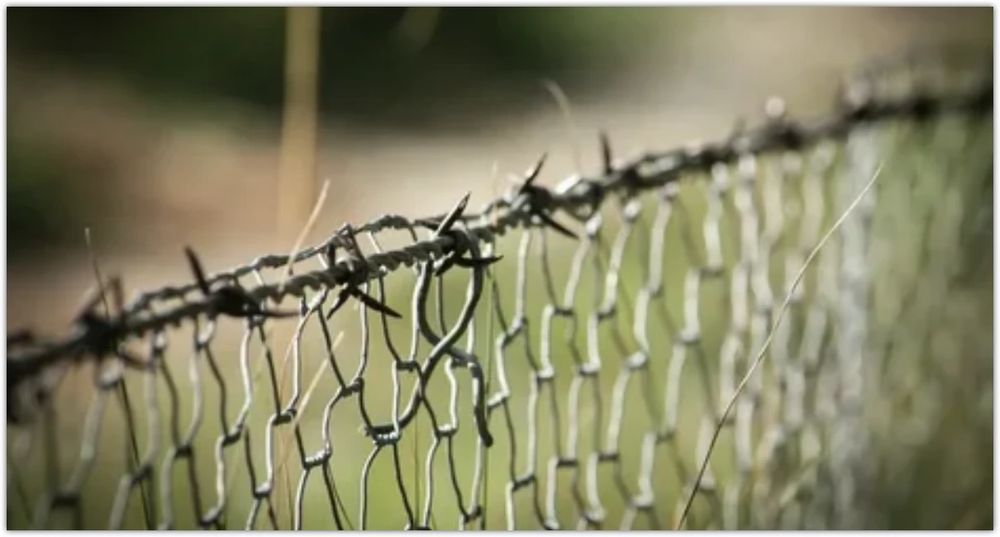
Метод полевой оценки качества колючей проволоки не требует специализированного оборудования. Достаточно иметь при себе минимальный набор инструментов. Практический контроль выполняют непосредственно на участке установки ограждения либо на складе поставщика.
Стандартный комплект для экспресс-анализа включает штангенциркуль, прочную веревку, груз известной массы и обычную лупу. Этот нехитрый арсенал позволит выявить большинство дефектов заводского происхождения. Важно проверять несколько отрезков из разных частей бухты.
Визуальный осмотр на дефекты плетения
Первичную оценку начинают с внешнего осмотра. Проволока раскладывается на ровной поверхности зигзагообразно для удобства исследования. Свежесть металлического блеска свидетельствует о качественном покрытии.
Проволока-основа должна иметь равномерный диаметр по всей длине. Отсутствие перекрутов и заломов — обязательное условие качественного изделия. Проверка выполняется путем протягивания отрезка между пальцами с легким нажимом. Любые утолщения или истончения немедленно обнаруживаются.
Шипы на проволоке проверяют на правильность формирования. Скрутка должна быть тугой, без люфтов и проскальзываний. Шип, качающийся на основе, — явный признак брака. Для проверки надежности крепления колючку берут за шип и встряхивают. Ослабленные элементы создают характерное дребезжание.
Оцинкованное покрытие исследуют на равномерность. Пятнистость, участки с разным оттенком свидетельствуют о нарушении технологии. Капли и наплывы цинка формируют коррозионные ячейки — в этих местах начинается ускоренное разрушение покрытия.
ПВХ-оболочка проверяется на эластичность и целостность. Надрезов, пузырей и смещений быть не должно. Качественная оболочка плотно прилегает к металлу основы. Для проверки сцепления покрытия с проволокой достаточно надрезать пластик и попытаться отслоить его пальцами — сопротивление должно быть значительным.
Измерение усилия на разрыв в полевых условиях
Простейший полевой тест на прочность выполняют методом подвешивания груза. Отрезок проволоки длиной около метра закрепляют одним концом на неподвижной опоре. К другому концу крепят тарированный груз.
Нагрузку наращивают ступенчато. Для проволоки диаметром 2 мм начальная нагрузка составляет 20 кг. Если деформация не наблюдается, груз увеличивают еще на 10 кг. Колючка из низкоуглеродистой стали выдерживает нагрузку 45-50 кг без остаточной деформации.
Скручивание — эффективный тест на пластичность. Два отрезка проволоки длиной 20-25 см скручивают между собой. Качественный материал выдерживает не менее 15-20 полных оборотов без признаков разрушения. Низкое количество оборотов до разрыва указывает на перекаленность материала.
Прочность сварных соединений проверяют методом отгиба. Сварной шов нагружают рывком в сторону, перпендикулярную оси проволоки. Качественное соединение не должно разрушаться или образовывать трещины. Разрыв соединения при небольшом усилии говорит о нарушении технологии сварки.
Тест на коррозионную стойкость займет больше времени. Образец опускают в пятипроцентный раствор поваренной соли на 48 часов. После извлечения и просушки проволока осматривается с помощью лупы. Допускается незначительный белый налет — продукт окисления цинка. Появление бурых пятен — признак низкого качества защитного покрытия.
Распространённые нарушения при производстве
Производство колючей проволоки — процесс технологически сложный. Компании порой экономят на сырье и технологиях. Эта практика приводит к выпуску продукции, не соответствующей заявленным характеристикам.
Бюджетные производители часто нарушают требования ГОСТов. Экономия на материалах и упрощение производственных операций снижает себестоимость, но серьезно ухудшает эксплуатационные характеристики. Выявить подобные нарушения без специального оборудования непросто.
Система сертификации должна обеспечивать барьер для некачественной продукции. Но сертификаты часто оформляются формально. Реальное качество изделий порой далеко от заявленного в документации. Проблема усугубляется тем, что большинство потребителей не имеют возможности проверить соответствие продукции нормативам.
Несоответствие заявленной маркировке
Самое распространенное нарушение — несоответствие диаметра проволоки заявленной маркировке. Заявляют 2,0 мм, а фактически используют 1,8 мм. Эта разница незаметна на глаз, но критична для прочностных характеристик. Снижение сечения всего на 10% уменьшает прочность на 20%.
Маркировку часто наносят неполную или неразборчивую. Отсутствие обозначения завода-изготовителя, даты производства, номера партии — признаки продукции сомнительного происхождения. Потребитель не получает информации для обратной связи при обнаружении брака.
Встречается подмена марки стали. Вместо низкоуглеродистой проволоки из стали С1 используют более дешевую марку БСт1. Внешне они неразличимы, но БСт1 имеет худшие механические свойства. При изгибе такая проволока легче ломается, а при растяжении раньше теряет форму.
Стальная проволока должна проходить термообработку. Отжиг снимает внутренние напряжения и повышает пластичность. Недобросовестные производители пропускают эту операцию. Экономия незначительна, а качество падает драматически — проволока становится хрупкой и подверженной излому в местах скрутки.
Снижение коррозионной стойкости
Цинковое покрытие — главный защитный барьер против коррозии. Заводы-производители иногда наносят слой в 1,5-2 раза тоньше требуемого. Вместо положенных 40-50 мкм наносят лишь 20-25 мкм. Визуально разница незаметна, но срок службы сокращается в несколько раз.
Технология цинкования тоже важна. Горячее цинкование формирует многослойное покрытие с диффузионной зоной. Гальваническое — только поверхностный слой. При вибрации или механическом воздействии гальванический цинк легко откалывается, оголяя металл основы.
Недобросовестные производители экономят на флюсах при цинковании. Применение некачественных флюсов приводит к неравномерному покрытию. Возникают участки с разной толщиной цинка. Именно в этих местах начинается преждевременная коррозия. Такие дефекты проявляются уже через 3-6 месяцев эксплуатации.
ПВХ-покрытие требует особого контроля качества. Распространенное нарушение — использование вторичного пластика без УФ-стабилизаторов. Такое покрытие растрескивается под воздействием солнечного света уже через сезон. Первичный ПВХ с УФ-добавками сохраняет эластичность не менее 7-10 лет.
Существует проблема адгезии пластикового покрытия к металлу. При нарушении технологии нанесения между ПВХ и проволокой образуются полости. Влага проникает через микротрещины и вызывает подпленочную коррозию. Внешне покрытие выглядит целым, но под ним металл уже разрушается.